Long-Range Exploration UAV
The Sweepwings Dreadnought
UAV’s have huge potential - I believe more so than manned aircraft due to the lack of constraints around carrying humans. Search and rescue, surveying, delivery, defence, videography, the list goes on. During the winter of 2018, I designed, prototyped, and built an 82” flying wing that was designed to fly for more than an hour and reach a kilometre in altitude.
If on mobile, turn your phone sideways to view the image below:
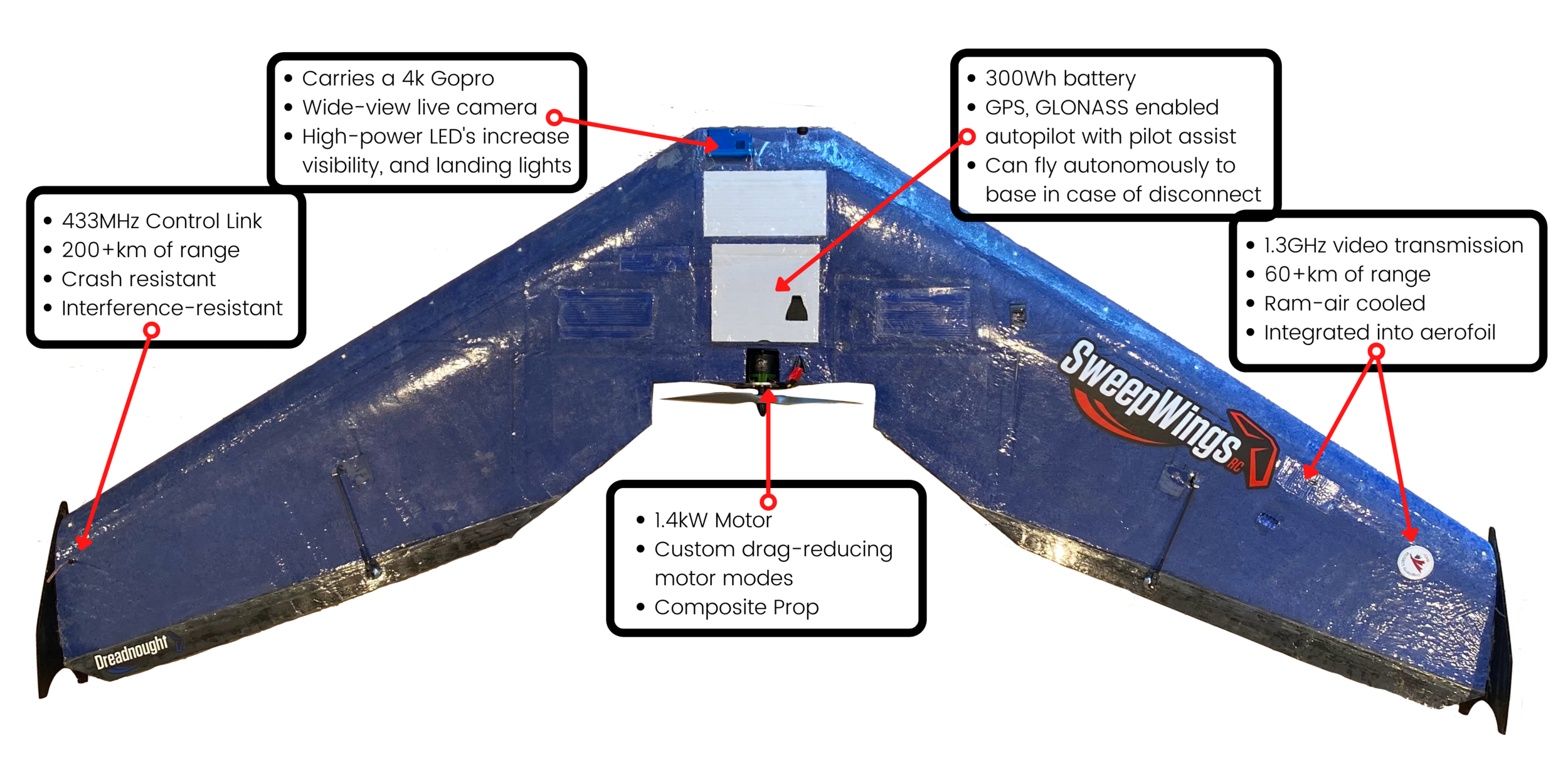
Challenges
-
Materials.
All I had access to was foam and laminate - much heavier than composite materials. I got around this problem by innovating a new construction method that yielded better crash protection with minimal weight penalties by making a derivative of a stressed-skin design.
-
Energy Storage.
Ideally, for this application Li-Ion would be the battery of choice due to their high energy density and minimal weight. Due to budget constraints, LiPo batteries were used which weigh more but are better suited to high amperage applications and cost less than Li-Ion.
-
Aerofoil Design.
In order to generate sufficient lift but cruise efficiently, a compromise was chosen in aerofoil design that used a thicker, washed-out, high camber aerofoil close to the wingtips, while a skinnier, more symmetrical aerofoil was chosen for the wing root and “fuselage” to reduce drag.
-
Budget Constraints.
A student budget severely limits the affordable components to use in the design. At the time of construction, no major drone companies had begun shipping an off-the-shelf long-range FPV system. This meant a clean-sheet design for the control and video transmission systems - an interesting challenge.
-
Power System.
With this project, failure was not an option. Using three onboard batteries created redundant power sources to protect against mid-air failures. The autopilot and control circuits were also electrically isolated from the motor power circuit, further decreasing the likelihood of catastrophic system failures.
-
Autopilot.
Using a well-known RC flight computer combined with some custom coding, I designed a full-capability autopilot that could follow waypoints, headings, and even return home automatically in the event of a video or control-link failure. This system also handled all the onboard mixing for the flight controls, making an inherently unstable flying-wing design operate completely hands-free.
Documentation of Build Process
First look at custom-designed wing in segments
Drafting structural and wiring schematics for use in CofG analysis and ensuring space in airframe for desired components

First bays cut into foam, checking fit with autopilot unit. Carbon and fibreglass spars can be observed "sunk-in" perpendicular to wing chord
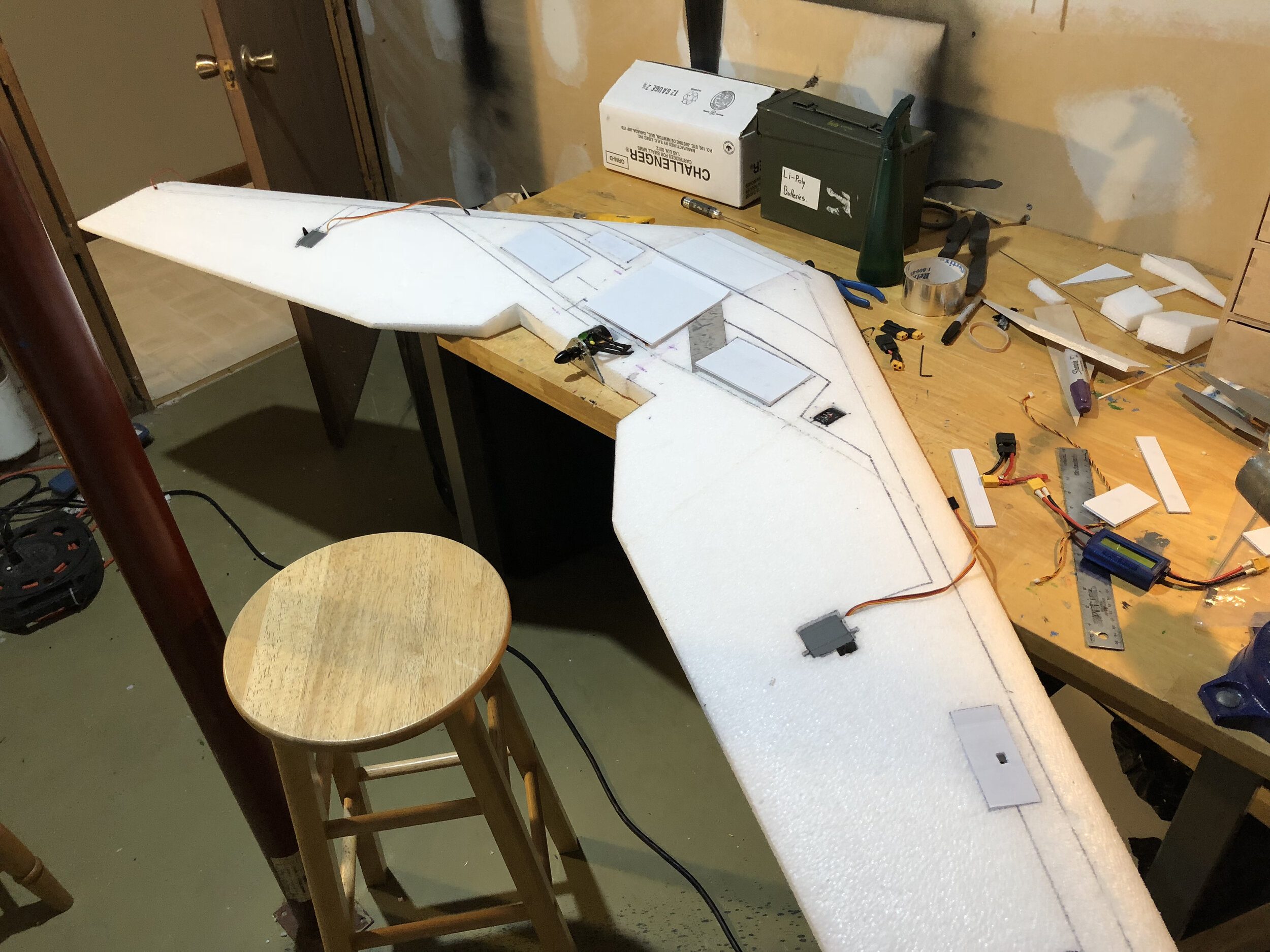
Power and control systems installed, starting preliminary thrust tests to choose best propeller for desired flight envelope
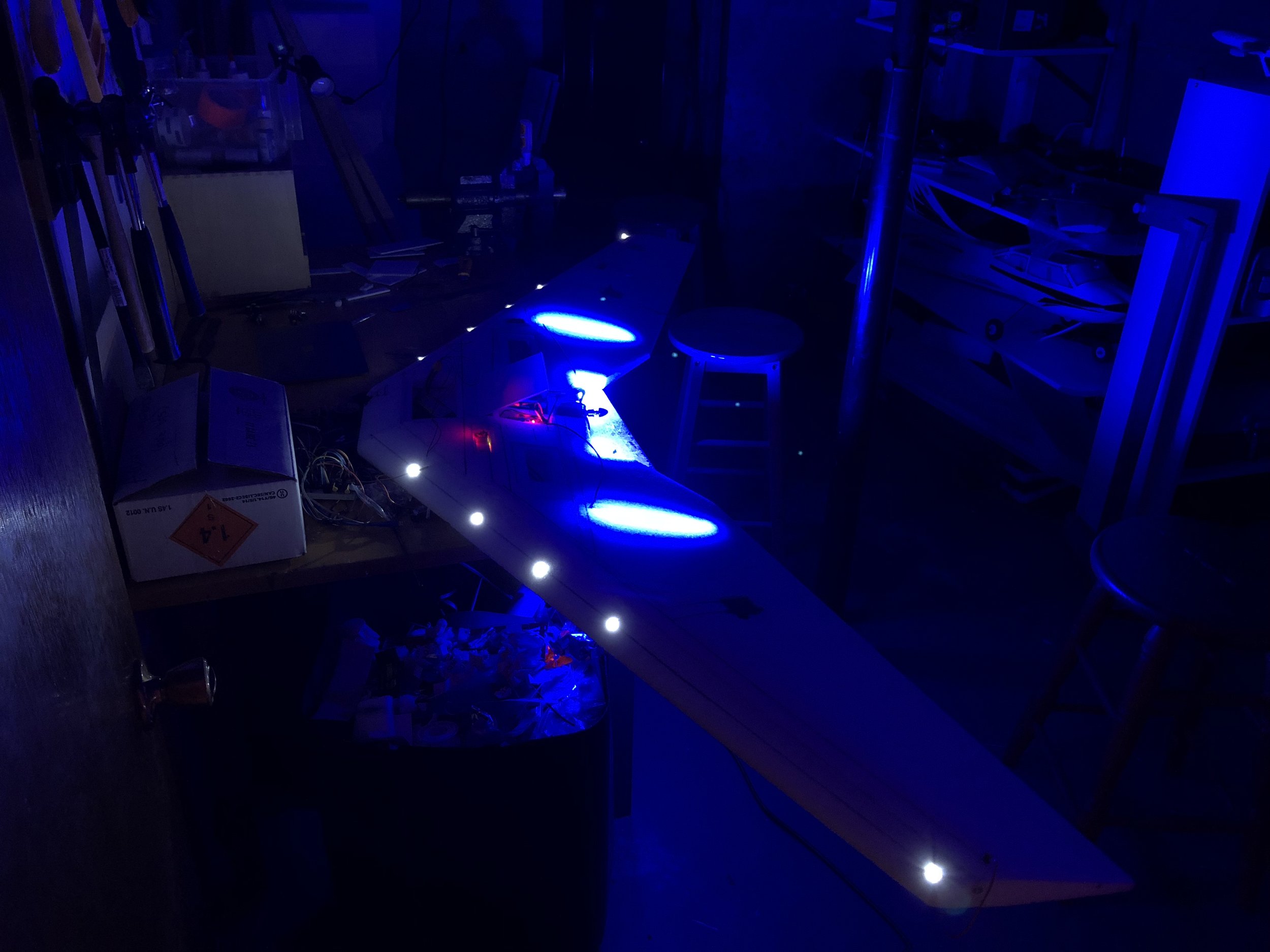
LED's installed for visibility completely inside structure, reducing drag while lighting up airframe
All components installed and tested, first coat of paint in progress, with laminating of airframe to follow
Final wiring arrangement of flight control and power systems inside aircraft's centre hatch, taken 15 minutes before maiden flight
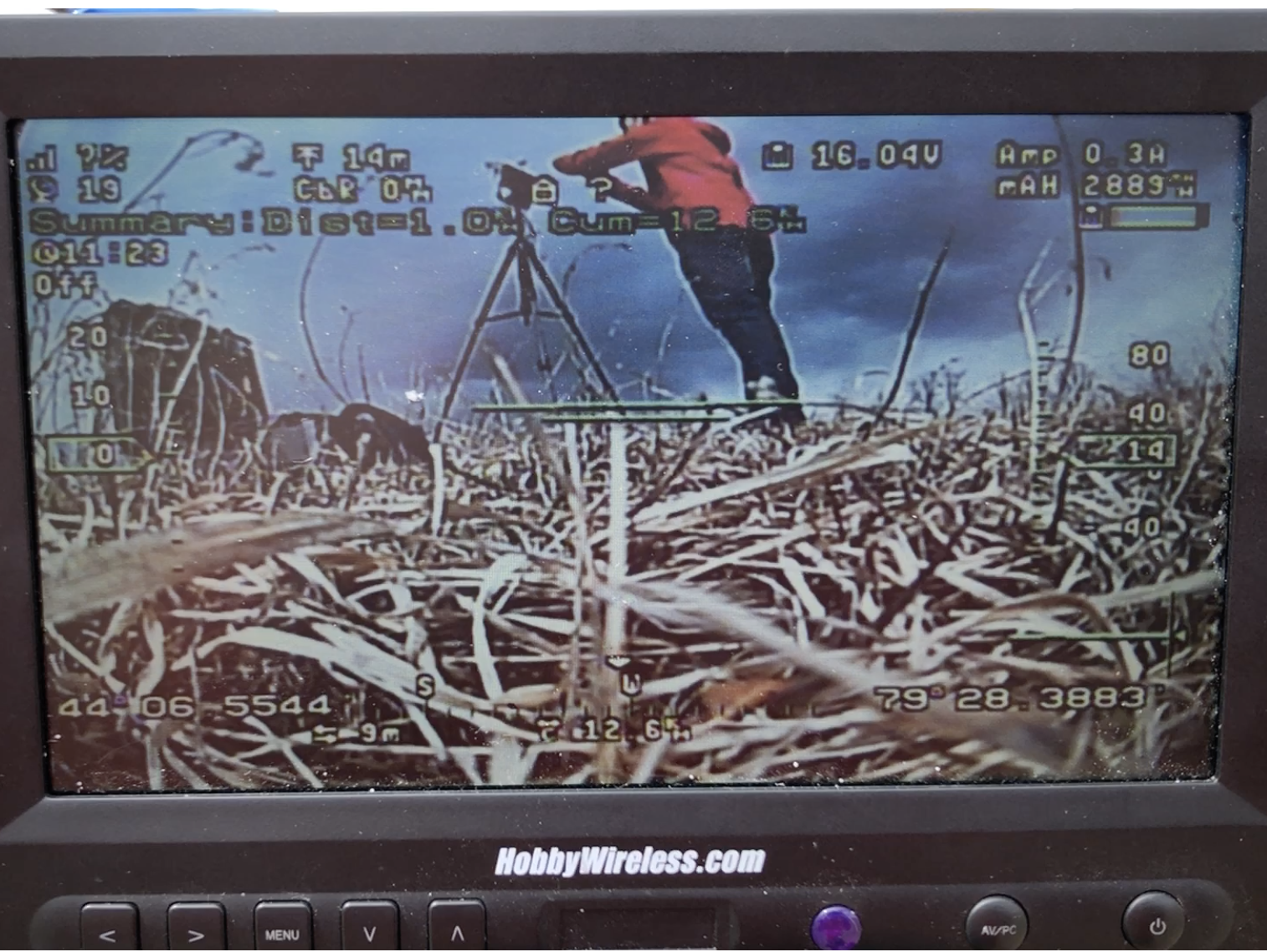
View from UAV's onboard camera as seen by ground control station - Altitude, Ground speed, amps consumed, amp draw, compass heading, etc... can all be viewed from this display
Maiden Flight.
It’s a great view from over a kilometre up…